Martin GPCE Inception Maple Debuts
The innovative Martin GPCE Inception Maple breaks new ground
.
Environmentally friendly woods and enhanced bracing marry with hopes for a future of sustainable, beautiful music
SEE THE FULL REVIEW WITH VIDEO HERE!
Incept Date: 01092024
Place of origin: Nazareth, PA, USA, Earth
Launched toward the future with appropriate celebration at C.F. Martin & Co., established in 1833 and boldly venturing into new territory in 2024, the Martin GPCE Inception Maple is an acoustic-electric guitar made in Martin’s Grand Performance body size with a Cutaway treble bout, representing the inception of a new Inception Series of Martin guitars that will feature domestic American tonewoods including Maple, in combination with environmentally sustainable tonewood from abroad, and the latest tone-enhancing technology inside the sold wood sound chamber.
In this case, the top is made from FSC certified European spruce. FSC standing for the Forest Stewardship Council, the world-wide entity assuring consumers that these certified natural resources were obtained from forests that are manged in an environmentally-friendly way with an eye on sustainability and with the greatest respect for the residents living within the forest.
The back and sides are made from maple grown in the USA, with a center plate of black walnut on the back that likely adds some tonal coloring to the voice of the instrument. Walnut is often described as a cross between mahogany and rosewood, but deserves its own place in the pantheon of true tonewoods that generate a pleasing sound capable of creating beautiful music. The fingerboard and bridge are also made from black walnut, as is the body binding and the decorative face plate at the front of the headstock.
This back does not have the usual alternating three-wedge shape of a Style 35 Martin. Instead, the center plate has a gentle curve to it. This is but one new aesthetic change from typical Martins.
While the back, sides, and top feature a new “amber fade” sunburst under a satin finish, the final production model retains important features of the Standard Series, like solid tonewoods throughout and the traditional, full-size dovetail neck joint. It also has the full complement of scalloped braces on the inside of the soundboard, except for a most unusual top plate that is only on the bass side of the upper bout.
However, this version of the traditional Martin-invented X-bracing is enhanced with a honeycomb of empty space, where mass was removed from the struts of the otherwise solid spruce X brace and the large traverse brace on the opposite side of the sound hole.
(click to enlarge photos)
![]() |
![]() |
![]() |
The purpose of this laser-cut spacing is twofold. It increases the flexibility of the bracing around the sound hole while maintaining a structural integrity that keeps the top from collapsing from the pounds of tension brought to bear on the soundboard by the taught steel strings. It is an achievement of engineering both elegant and practical, invented centuries ago for weighty yet airy stone structures like the cloisters of medieval abbeys and cathedrals. But here it is brilliantly applied in miniature for a light, solid-wood soundboard of a world-class musical instrument.
Another significant enhancement is implementation of “sonic channels” cut into the solid spruce soundboard, around each brace and tone bar, and along most of the circumference of the soundboard. This allows the sold top to respond more-easily to the vibrations passing through it.
Soundboard channeling is an idea that has been explored by other guitar makers, but not nearly to this extent or in the same patterns. This feature also appears around the back braces that have been redesigned to allow the back to contribute to sonic resonance, not just passively reflect the sound waves generated by the spruce top.
While I could go on about the development of this project based on insider tidbits, I felt it best to prevail upon the man inside Martin Guitars who knows more about it than anyone, Vice President of Product Management Fred Greene. Fred was happy to share some exclusive insight with One Man’s Guitar about the evolution of the GPCE Inception Maple in his own words, and how this exciting new Martin guitar is but the vanguard of the bold future ahead for America’s most venerable musical instrument maker.
OMG: How long has this project been in the works?
FG: The project has been in the works for about 18 months.
OMG: What were the origins of this new model?
FG: It started with a desire to highlight the possibilities of sustainable domestic hardwoods in guitar construction.
OMG: Martin has made some very successful models with sustainable domestic tonewoods, like maple and walnut, yet not many, and nothing with this combination of body size and tonewoods. What was behind the inception of the Inception?
FG: I knew we couldn’t simply make another maple Dreadnaught and leave it at that. It’s been done by us and others in the past. Too often big manufacturers get lazy and stop innovating. When that happens, new models can be met with a collective yawn from guitar players. I felt we needed to make changes in how we designed this musical instrument on a deeper level.
OMG: Well, nothing is boring about this new maple model! Who was the primary designer of the GPCE Inception Maple?
Like most projects at Martin, it was a team effort. But as the leader of the product team, I instigated a change in our approach stemming from my desire to show off the potential of these woods by combining the technology we have developed over the past 190 years with innovations we developed in the twenty-first century. That was the mission I tasked the team to embark upon.
Nate Hoffman, our R&D leader, took up the challenge and his team really dug deep and presented us with some cool concepts. Those concepts were discussed, massaged, prototyped, and eventually agreed upon by myself, designers Tim Teel and Rameen Shayegan, and the production team. We felt it was very important that we showed the world that Martin continues to innovate and explore the possibilities presented by a changing world of materials and technology.
OMG: How are the gorgeous, skeletonized braces created?
FG: The new braces are created using lasers. We realize we are not the first company to put holes in braces. Small one-off builders have done this in the past. However, I believe Martin is the first “major” builder to do it in a true product guitar. It was fun developing a weight-relieving pattern that was both visually appealing and strong.
OMG: How do they affect things like energy transference and tone production?
The general concept is simple. By lightening the weight of the braces, and consequently the top, less energy is required of the strings to move the top. Thus making the instrument more responsive and increasing sustain.
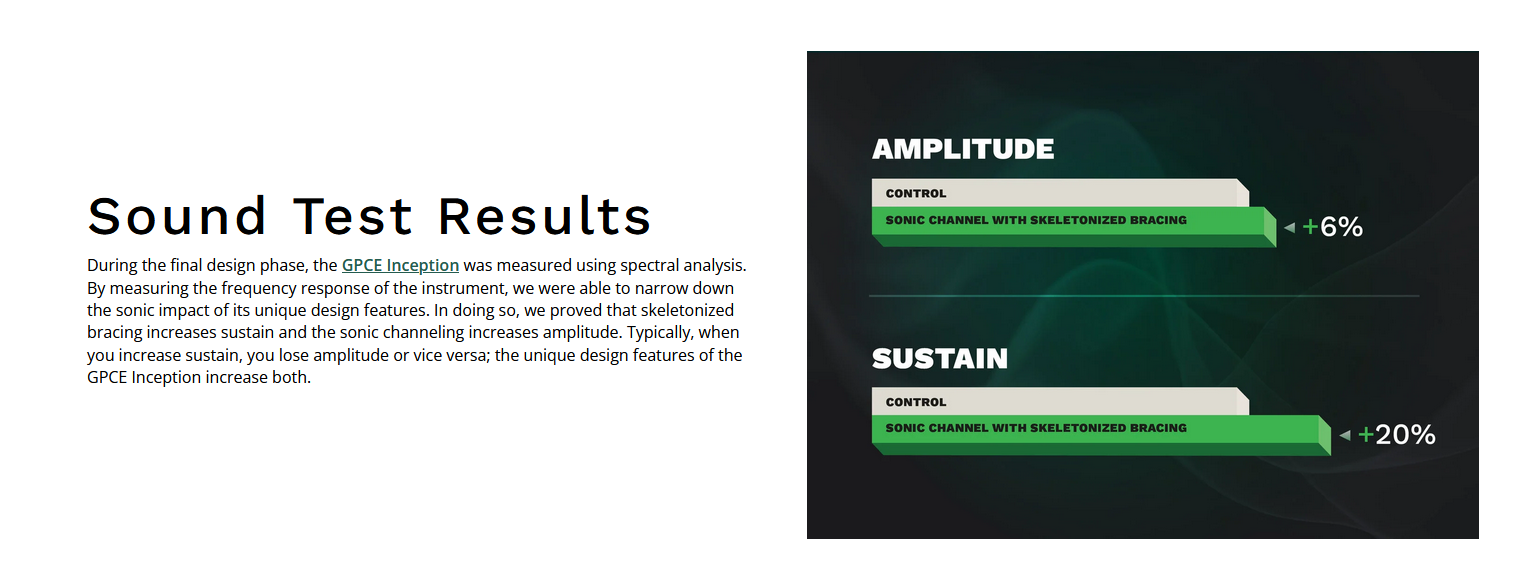
Maple tends to compress sound in acoustic guitars with traditional builds so that all you hear is the fundamental notes without any pleasant overtones. We wanted to allow the guitar to move a little more and offset some of that compression. We wanted to open it up. This bracing in combination with the new sonic channels set into the underside of the soundboard more than accomplished that goal.
OMG: Why the Grand Performance body size?
We saw this guitar as a stage guitar for a singer/songwriter and the GPC seemed like a natural canvas for something new. We thought if we started with a Dreadnaught or 000 it would simply draw too many comparisons to existing models that already have a very established sound signature. We didn’t think these traditional shapes would be the right formula or recipe for the player we were targeting.
OMG: Might we assume the new Marting GPCE Inception Maple is so named because this is the beginning of a new trend at Martin Guitar? Should we expect to see other models featuring domestic American tonewoods and the new bracing and sonic channels under the top?
You are correct that the Inception is the first of several new guitars that will be coming in the future using more sustainable woods. It’s exciting because these new guitars will allow us to offer new designs and hopefully give guitar players more options and sounds to explore.
Well, it’s been worth the wait to see the end results of this long-anticipated project. Now I have to wait a little longer to play and hear the finished product officially being released at the NAMM show on January 24, 2024.
Check out the Martins and More podcast where Spoon Phillips and Maury Rutch share even more information about the minds and muscles that created this super cool new Martin GPCE Inception Maple, below.